GT Workcells Are
Different
The popularity of Cellular Manufacturing and workcells
has grown, fueled by the adoption of the Toyota
Production System (TPS) and it's namesake, Lean Manufacturing. But, there are problems.
The
developers of TPS, Taiichi Ohno and Shigeo Shingo, were pragmatists. The evolution of TPS
was largely trial and error-- long on practice; short on theory. From their writing it is
evident that Ohno and Shingo had a wonderful intuitive grasp of the system but their
explanations of the why behind it are a bit muddled and somewhat rare.
As a result, much of what came from Toyota is in the
form of rules and edicts that reflect what worked and what did not. Rules and edicts also helped
propagate the system throughout Toyota and the supplier base.
The really big problem involves volume and variety.
Toyota's U-shaped, balanced workcells do not work when orders are unpredictable, routings vary
and work balance changes.
Group
Technology workcells manufacture many products that are similar, but not identical. In job
shop situations a cell may produce hundreds of different parts. Demand is often erratic and no
single part has enough volume for its own cell.
A more fundamental approach to cell design is necessary
and the results may look very different than the Toyota model. You can learn more about this
from our page on Workcell Design or by downloading
the workcell design chapter from Mr. Lee's next
book. We also offer a seminar on Cellular
Manufacturing.
Workflow
In a GT cell operations and sequence often vary. Some parts require machines 1,2,7 and 9 in
that order. The next part may require machines 1,2,3 and 6. The average work time at each
machine varies. Work times also change from part number to part number.
Process Technology
GT workcells usually favor smaller-scale, less automated process technologies that changeover
easily and fit the lower volumes. Machine shops are an exception. CNC machining fits very well
with GT cells. CNC technology does not really cut metal faster, it reduces setup and combines
operations.
Batch Size
As in the Toyota system, small batches are better. But the high variety may not allow the
kind of setup reductions that we can achieve with only a few products.
Moreover, customers often order in lots and the batch size must reflect this. As a result,
production batches tend to be larger and more varied than in a Toyota cell but still much
smaller than in functional arrangements. For more on this, see
"Lean Lot Sizing."
Transfer Batch
The transfer batch or internal lot size also tends to be larger than in Toyota cells. This is
the number of pieces moved together between operations. The inventory in the transfer batch must
be large enough to balance operations within the cell.
GT cells are often larger than Toyota cells. The greater distances between workstations
require a larger transfer batch to amortize travel time over more pieces.
One piece flow may not work.
Layout
Toyota strongly favors U-shaped layouts that give direct material flow and allow operators to
balance their work in several ways. This is
very sensible when the routes are all identical.
GT cells should be designed around the most common workflow routes but they must also
accommodate less common routings. This gives rise to unusual arrangements such as L-shapes and
X-shapes

|
Group Technology Workcell Example
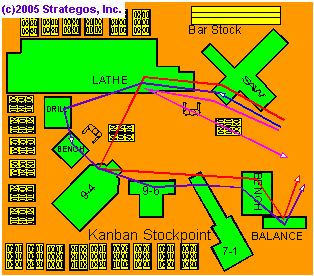
This cell has the classic U-shape but it does not operate like a Toyota Cell. This cell
produces about 85 different turned parts. These are shafts and shafts with integral pinions
and/or splines. Arrows show the sequence for three of these many parts.
All parts have dedicated carts for handling and storage. They serve as material handling
devices, containers and kanban. Perimeter carts are a kanban stockpoint.
The internal lot size (transfer batch) is one cart (16 parts). External lot size varies from
16-48 parts in multiples of 16.
Work times are highly variable and unbalanced. The hobbing machine (7-1) is extremely slow
while the NC lathe is fast. The product mix was carefully selected to include some parts that
require hobbing and many others that do not.
Operators schedule their work from kanban signals. They must schedule non-hobbed parts
immediately after a hobbed part. If they did not, the slow hobber would bring output to a crawl.
They may have 2-3 part numbers underway at the same time.
Operators stay alert because the variation in cycle time means that machines finish at
unforeseen moments. Operators constantly move from one machine to another, loading and
unloading. Small queues highlight temporary bottlenecks which get special attention.
Some drilling and milling might have been done on the NC lathe using special attachments.
But, we chose to make these secondary operations to reduce machine time on the lathe. These
operations occur internally to lathe turning and cell output increases as a result.
While the whole arrangement may seem like a recipe for chaos, it actually works quite well.
It is not nearly as smooth as a classic Toyota cell but it is far better than the genuine chaos
of a functional layout.
A lot depends on the operators. Here, they were skilled and experienced machinists. With
kanban, we knew they could figure out what part to run.
Another
GT Workcell Example (Assembly/Fab)
|