Total
Productive Maintenance (TPM) is the maintenance sub-system of Lean Manufacturing. TPM improves
manufacturing performance by reducing cost, improving quality and increasing productivity.
As with other parts of Lean, TPM borrows tools and techniques from other disciplines as well
as previously developed and proven maintenance techniques. The combination, integrated as a
system and further integrated with the larger Lean system, produces results far beyond the
individual techniques; i.e., the system is more than the sum of its parts.
Losses & Cost Avoidance
In one sense, everything in maintenance is waste since none of it directly contributes to the
customer's needs and wants. While a perfect factory with perfect equipment would need zero
maintenance effort, real factories and real equipment need maintenance to function. Without it,
they create further waste in lost time and defects. The objective of TPM is to minimize
the total waste or, in TPM terms, loss.
Maintenance-related losses come in many forms. Accounting systems show some costs (losses)
but others remain hidden as in figure 1. For example, the exact cost of maintenance labor and
parts is easy to track. The cost of a defective part is somewhat easy to track but the
"commotion cost" of the defect is nearly impossible to track and usually much greater. For a
similar
example, see: The True Cost of Defective Quality.
The trick is to find the balance between direct maintenance expenditures and the hidden costs
while ensuring that maintenance resources are effectively used. Analytically and quantitatively,
this is very difficult. From this author's experience and observation, however, few (if any)
factories spend too much on maintenance. Most operate far to the left on the total Cost Curve of
figure 2. Well-managed maintenance is nearly always a good investment.
The Origins of TPM
The demands for predictable machine performance in Lean Manufacturing led to the development
of TPM. Early on, the people at Toyota must have realized that many quality problems and setup
problems originated in poor maintenance. Total Quality Techniques, Statistical Process Control
(SPC) and problem solving teams transferred well to maintenance issues. Reliability Centered
Maintenance (RCM) also contributed. Reliability Centered Maintenance developed from the
military's development of Reliability theory which, in turn, came from statistical theory.
Statistical theory also contributed to the development of SPC. The use of problem solving teams
came from Eric Trist's Socio-Technical Systems
as well as from Reg Revans' Action Learning.
Figure 3 is a simplified summary of TPM's development.
Results
Some years ago I was Maintenance Superintendent in a large, 100-year-old steel foundry. We
employed most of the principles, tools and techniques of TPM long before they had names. The
results were excellent. For example, our average downtime on overhead cranes went from about 17%
to 2.5%. Other major equipment showed comparable results. Here are some other results reported
by industry:
-
MRC Bearings reduced unplanned downtime by 98% in one cell and 99% in another - all
within one year.
-
Monsanto runs their three-year old TPM start-up plant at 97% on-stream time while most
other units run between 85% and 90%.
-
3M reduced their maintenance cost by 60% within three years.
-
DuPont reduced off-quality by 69% and improved capacity by 29% in three years.
-
Harley-Davidson estimates that the ROI from TPM has been ten-fold to the cost of
implementation.
-
Kodak reported a $5 million investment in TPM that resulted in a $16 million increase in
profits.
|
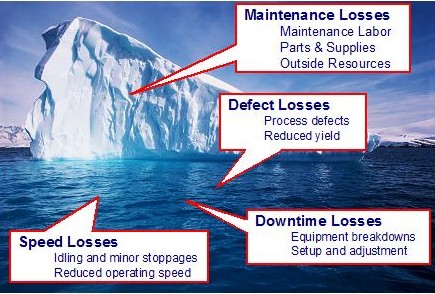
Figure 1 Maintenance Losses
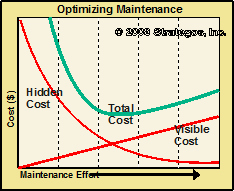
Figure 2 Optimizing Maintenance Cost
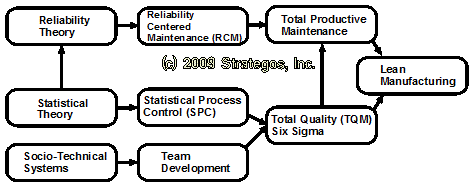
Figure 3 Origins of Total Productive Maintenance
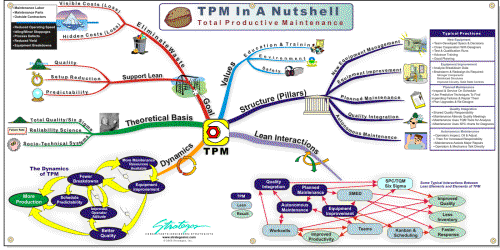
TPM In A Nutshell
(Click to Enlarge)

|