Total Productive Maintenance is often
presented as a series of pillars supporting Lean Manufacturing and resting on a foundation of
education and training. Below this is the attitude of environmental responsibility and safety.
Figure 5 illustrates. This representation is adequate as a starting point. However, TPM, like
Lean itself, is a dynamical system and cannot be fully understood with a static model.
Supporting Lean
Maintenance enables and supports Lean
efforts in at least three major ways: Quality, Setup Reduction (SMED) and predictability. In
turn, other Lean elements support TPM through Workcells, Teamwork and Problem-solving.
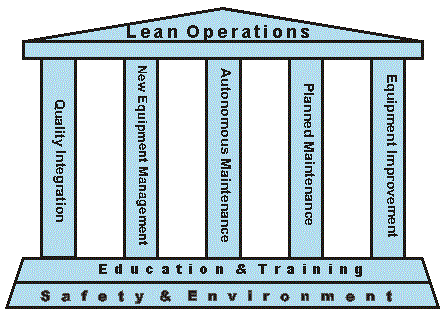
Figure 5 the Pillars of TPM
Several
versions of the "Pillars" attempt to represent
Total Productive Maintenance
|
The Foundations
Education & Training-- Education,
training and investments in people characterize all aspects of Lean. In the maintenance area,
they are even more important because of the specialized knowledge required on typical
manufacturing equipment. This is one of the foundation stones of TPM. Without it, the pillars of
TPM will have limited impact.
Safety/Environment-- Underlying even the
training and education piece are the more fundamental values of responsibility to the
environment and safety for employees. One important reason is simple: it is the right thing to
do.
A more pragmatic reason involves
motivation. Most people want to be a part of something larger than themselves; appeals to higher
motivation bring involvement and commitment. It is difficult to argue against safety and a
common commitment to safety can be a bond that brings people together on other issues.
Autonomous Maintenance
Autonomous maintenance is the concept
that the people who operate a machine should maintain the machine. The degree of autonomous
maintenance depends on the level of training and the abilities of operators. It often starts
with basic lubrication, cleaning and inspection and then graduates to minor or even major
repairs.
For example, in the foundry where this
author worked, machinists repaired and overhauled their own machine tools. A trained and
competent machinist is certainly capable of overhauling a gearbox. And, as the users, they
tended to know the equipment intimately. In the military, everyone cleans their own weapon. When
their life depends on proper functioning, people take more care.
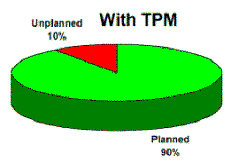
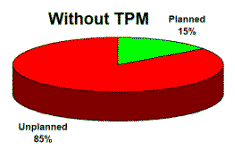
Planned Maintenance
Charts show the proportions of planned and
unplanned maintenance with and without TPM.
|
Autonomous maintenance frees resources
in the maintenance department for the other activities such as equipment improvement or major
overhauls. It amplifies the maintenance efforts and involves the operators who then take better
care of the equipment.
Planned Maintenance
Planned maintenance is the deliberate planning and scheduling of maintenance activities as opposed to
reacting to breakdowns and emergencies. A maintenance department that uses TPM effectively
generally devotes less than 10% of its labor hours to such unplanned activities.
Without TPM it is not unusual for 80%-90% of the labor to be unplanned. Unplanned maintenance is a
strong indicator that prevention and improvement programs are non-existent or ineffective. In
addition, high percentages of unplanned maintenance creates problems. For example:
-
Huge inefficiencies in maintenance
labor.
-
Confusion and disturbance in
scheduling, production and other areas.
-
Morale problems.
|
Equipment Improvement
Improving equipment constantly is a major part of TPM. This author witnessed an outstanding
example of this some years ago at Toyota's Kamigo Engine plant. Toyota was using the same type
of American equipment that I had seen at Ford Motor Company years earlier. However, Toyota's
equipment was so reliable that it ran with far fewer people and far better quality. For more on
this see Kamigo engine Plant, 1985.
Most production equipment has not had the extensive design, testing and development common in
mass-produced products such as automobiles. Accordingly, there are many deficiencies that may
not be evident when the equipment first goes into service. In addition, each manufacturing plant
and its products tends to be different and can benefit by design changes that adapt the machines
better to their individual situations.
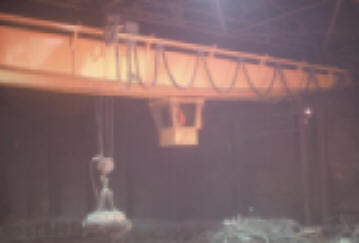
Figure 7 Rebuilt & Improved Overhead
Crane
This 20-ton crane was originally built in 1929.
Fifty years later is was structurally sound but had an outmoded and troublesome
electrical system. It was retrofitted with all-new controls and the trolley wires were
replaced with a modern flexible cable system clearly seen in the photograph. It will
probably outlast a brand new crane.
|
Older equipment does not necessarily have to be replaced. In many cases, it can be upgraded
and overhauled and made better than new. In our steel foundry, we did this with fourteen of our
overhead cranes. Some were upgraded and re-rated for heavier capacity. All were fitted with new
controls, structural deficiencies were fixed and the cranes made better than new. Several of
these cranes were over 45 years old.
New Equipment Management
New equipment management is related
somewhat to equipment improvement. It refers to the careful design, selection and testing of
equipment. The purpose is to ensure a smooth commissioning process with minimal design defects
and problems. New equipment management includes vendor selection, evaluating options for
maintainability, training personnel in advance and other common-sense techniques.
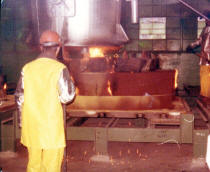
Debugging Rollover
First Pour
Figure 8 Startup Of No-Bake Foundry
New equipment management enabled a smooth startup
for this no-bake foundry operation. Thirty five years later it is still in production.
|
Process Quality Management
In TPM making the equipment run is only
part of Maintenance's job. Ensuring that the equipment is capable of producing parts well within
the tolerance range (process capability) is also a primary responsibility.
Worn bearings and ways, undo vibration,
bent shafts and multiple other maintenance problems contribute to the gradual deterioration of
process capability. With constant use, machines still run but become "finicky." For example, a
particular machine shop lathe that the author recalls could only be run by a particular
operator. He was the only one who knew exactly where the ways were worn and how to compensate.
Maintenance often has a significant
impact on setup time. Worn or broken equipment is often difficult but not impossible to setup.

|