What Is A Socio-Technical System?
In the
early 1950's Eric Trist and the Tavistock Institute studied the English coal mining industry
where mechanization had actually decreased worker productivity. Trist proposed that
manufacturing (and many other) systems have both technical and human/social aspects that are
tightly bound and interconnected. Moreover, it is the interconnections more than individual
elements that determine system performance.
The technical system includes machinery, processes, procedures and a physical arrangement. We
usually think of a factory in terms of its technical system.
The social system includes people and their habitual attitudes, values, behavioral styles and
relationships. It includes the reward system. It is the formal power structure as depicted on
organization charts and the informal power structure deriving from knowledge and personal
influence.
Mechanization In The English Coal Mines
In the coalmines, mechanization had broken up tightly knit teams that had previously
performed the entire extraction process from blasting to hauling to sorting.
-
With mechanization, different people performed the various steps of extraction on
different shifts and this caused coordination problems.
-
The equipment was so loud people could not communicate and this inhibited teamwork and
team development.
-
The pay system went from a group incentive system to an hourly wage system and this
destroyed monetary motivation.
-
People felt alone, isolated, and unappreciated deep in the earth. This destroyed the
powerful intrinsic motivators of pride, satisfaction and belonging.
The overall result for the English mining industry was decreased productivity and labor
strife.
|
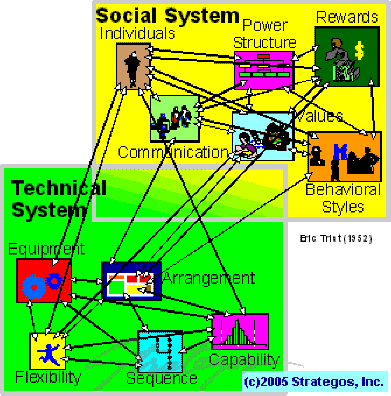
Joint optimization is the goal of socio-Technical design. For example, a manufacturing
workcell that requires high teamwork will not produce in an environment of suspicion and
command/control. A self-directed work team will be ineffective when the layout of their area
prevents communication or does not require cooperation. The social and technical systems must
integrate and assist one another.
When Lean Manufacturing goes awry, the root cause is often failure to appreciate the nature
of the system. The socio side is often (though not always) neglected. Team development, training
and culture are just as important as fast setups and cellular arrangements.
|