Implementation Project Example
Here is a very simple example of a Phase I implementation that illustrates the principles. It
anticipates three workcells. Each workcell will require
Rapid Setup (SMED),
kanban production control,
Total Quality and
Team development.
In addition, the plan anticipates a more general supplier development effort that, eventually
brings suppliers into the kanban system.
The Gantt chart shows a timeframe for each activity. The workcells are sequential. The more
general supplier development and kanban is essentially separate.
This schedule limits the number of tasks that a particular department must undertake at any
one time.
|
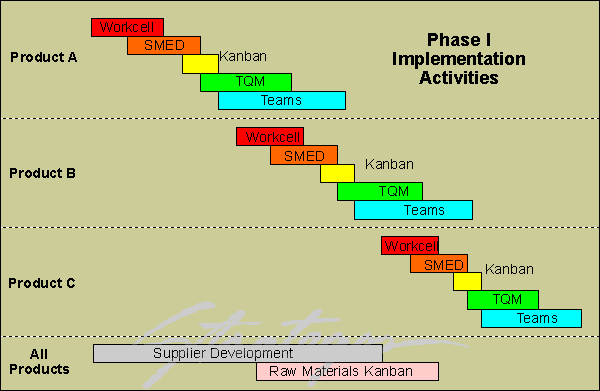
|
Departmental Loading Chart
The chart shows, for each department, tasks that require their heavy involvement. Note that
no group has a heavy involvement with more that two simultaneous tasks.
Summary
Every Lean Manufacturing implementation is unique because every factory is unique. The
originators of Lean Manufacturing, placed in different circumstances, would have developed
different solutions.
The keys to success include: a fundamental approach, systems thinking, leadership, a flair
for strategy and recognition of the practical limits on resources.
|
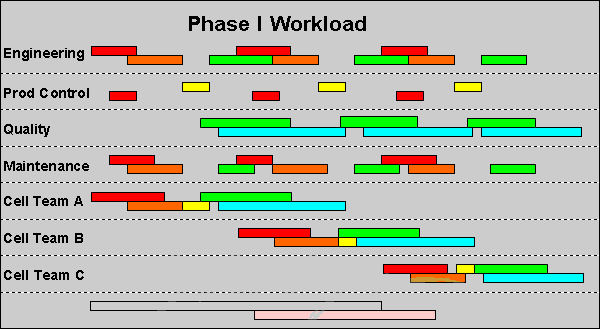 |