Events & Tasks
Here is an approach for launching a Lean Implementation in medium-size factories of 100-300
people. Larger factories require a more elaborate launch with formal change management
techniques such as Appreciative Inquiry, Future Search and World Cafe. Smaller launches might be
simpler.
Our approach combines theory and practice with training, guided strategy planning and a
Kaizen Event over 2-3 weeks. It enables the necessary individual and organizational paradigm
shift. This launch:
-
Provides an initial experience of a lean environment
-
Introduces basic principles, themes and elements
-
Provides a theoretical framework
-
Prepares for initial strategy development.
The deliverables include:
-
An Appreciation for present problems and future possibilities
-
Consensus for Change
-
Knowledgeable & Committed Steering Committee
-
An operating Workcell, Line or area
-
Initial Lean Strategy Statement
-
One-Year Implementation Plan
|
Future Search
We employ a variation of "Future Search" for instigating "whole system change." The
principles include:
-
A cross-section of people representing the entire system.
-
An learning environment where people experience the entire system in action.
-
A Focus on common ground and future action.
-
Enable participant responsibility for their own action plans.
Future Search fosters understanding, belief and commitment. It helps people to experience and
accept polarities and to bridge barriers. It changes the way people interact.
The Steering Committee
The Steering Committee provides guidance and resources for the Lean initiative. It has 10-30
people representing all levels of the organization and all important functional groups. It
includes people from Production, Scheduling, Human Resources, Maintenance, etc. as well as
factory workers, middle management and executives. If the company has a union, it should be
well-represented. The "whole system" is in the room and committed to the entire session.
|
Lean Launch Activities
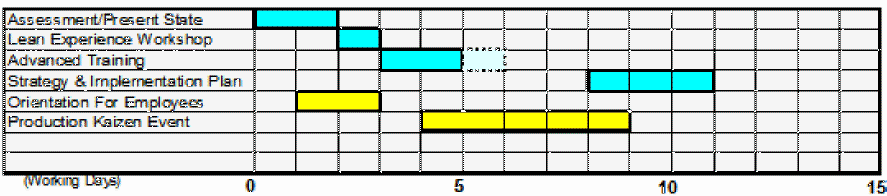
The activities and sequences on this Gantt chart are described below.
This schedule is somewhat flexible and may occupy a period of 2-6 weeks.
|
Assessment/Present State
In this informal workshop, the Steering Committee examines the present state of their
manufacturing system and benchmarks with respect to Lean principles.
More Info>>
Lean Experience Workshop
This workshop and simulation introduces Lean Concepts. Participants operate a simulated
factory and then redesign it with newly learned Lean Manufacturing principles. They operate
their new factory to measure, see and experience the results. It provides the emotional and
intellectual framework for understanding Lean.
More Info>>
Advanced Training
This workshop expands on those lean elements that will be most applicable during the first
year. It gives managers, engineers and others involved in system design adequate knowledge to
apply the elements in their factory. The content is determined with the client and usually
includes:
|
Strategy & Implementation Plan
In the Strategy & Implementation sessions, the Steering Committee develops their Lean
Manufacturing Strategy and an implementation plan for the next 12-24 months. This planning
identifies future training requirements, the sequence of events and those lean elements most
necessary for the product-process-market mix. The previous training gives participants the
intellectual knowledge for this task and the Kaizen Event provides experience.
Lean Manufacturing Orientation
Employees not involved in the other training session participate in a half-day orientation
course. In it, participants operate a simulated factory with Lego blocks. They redesign their
factory in stages, measure the results and learn underlying principles. The program includes
lecture, video and a lean simulation. The simulation is carefully designed in clear stages to
show the effects of each element. A rigorous debriefing ensures that participants internalize
the principles. More Info>>
Workcell Kaizen Event
In this 3-5 day Kaizen event, participants analyze an area or product line and design a
workcell. They implement many or all of the improvements identified in the analysis. They then
operate the line and demonstrate the benefits. A Strategos facilitator guides the event. The
objectives of this Kaizen Event are to:
-
Demonstrate effects of Lean
-
Improve productivity, quality and inventory
-
Provide Kaizen experience
-
Build a consensus for change
-
Build a constituency for change
|