How It Works
Kanban
scheduling systems operate like supermarkets. A small
stock of every item sits in a dedicated location with a
fixed space allocation. Customers come to the store and
visually select items. An electronic signal goes to the
supermarket's regional warehouse detailing which items
have sold. The warehouse prepares a (usually) daily
replenishment of the exact items sold.
In modern
supermarkets Kanban signals come from checkout scanners.
They travel electronically (usually once a day) to the
warehouse. Smaller stores still use visual systems.
Here, a clerk walks the aisles daily. From empty spaces
he deduces what sold and orders replacements.
Another variation is the bread truck. Here drivers
follow a fixed route from store to store. They have a
supply of bakery items in their truck. At each stop,
they examine the stock and replenish what has been sold.
Kanban scheduling in
manufacturing works in the same way. The essential
elements of a system are:
-
Stockpoint(s)
-
A
Withdrawal Signal
-
Immediate
Feedback
-
Frequent
Replenishment
Kanban Schematic
This graphic illustrates how a Kanban system
connects the upstream supplier or workcenter with a downstream user or customer. It
operates through a small stockpoint and a signaling system.
|
|
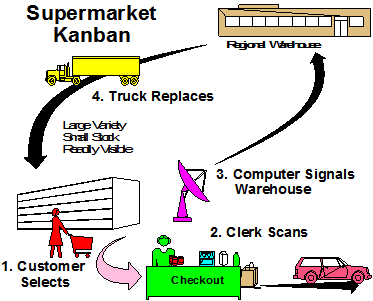
Kanban In A
Supermarket
The entire buy-replenishment cycle is 1-3 days.
Supermarkets have the highest inventory turnover of almost any business. One of several
legends says that the supermarket was the original inspiration for Kanban.
|
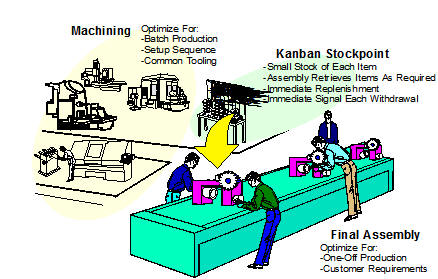
Kanban In Manufacturing
Here, the supermarket principle is applied to a
machining and assembly operation. Machining and assembly have very different
requirements and considerations for scheduling. Kanban compensates for these differing
requirements.
|
|