Lean and the Job Shop
Lean Manufacturing in job shop environments has an uneven record. There are some notable
successes, some disasters and many non-starters. We can add misguided perceptions about Lean's
applicability to the usual culprits of non-support and change resistance.
-
In some cases managers view Lean as a universal theory for all situations. Since much of
the lean literature derives from Toyota, they attempt to copy Toyota's practices without
question. In a job shop this can lead to disaster (See
Blitzing To Disaster). At best this means a lot of work with little result.
-
In other cases, managers recognize that "job shops are different" and then conclude that
Toyota's methods have no place in a job shop. Hence, the non-starters.
Actual situations are more complex and more subtle. At Strategos, we see differences in the
following areas:
-
Cellular Manufacturing
-
Group Technology
-
Value Stream Mapping
-
Kanban & Scheduling
|
-
Focused Factories
-
Work Standardization
-
Implementation
|
Cellular Manufacturing
Workcells
in a job shop are quite different than in a higher production facility. They may process
hundreds of different (although somewhat similar) items rather than the 3-4 items typical in
higher production facilities. The demand for the various items may vary considerably both
in pattern and overall volume. The process may vary significantly both in the routings and in
tools and fixtures. Work times, setup times and lot sizes vary over a wide range.
Job shop workcells sometimes appear similar to high production Toyota-type cells but they
function differently. One Piece Flow may not be applicable and internal lot sizes may be larger.
The matching of product groups to workcells becomes difficult. Several jobs may be in process
simultaneously within the cell. Quality approaches are often substantially different with more
emphasis on operator knowledge and Attribute Charts rather than mistake-proofing and Variables
Control Charts.
All of this requires a far more rigorous design process based on fundamentals rather than
cookbook formulae. Our pages on Workcell Design can
help.
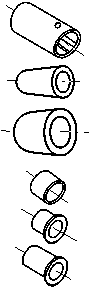
GT Part Family
|
Group Technology
Group Technology (GT) is the art and
science of grouping items according to similarities in relevant characteristics. Generally in
manufacturing, this means similar characteristics in process routings and sequences. Such
grouping is one of the first steps in a rigorous cell design process. It defines what parts go
in which cells.
In high-volume, low-variety production, part groups are often self-evident. At most some
discussion and informal thought may be necessary. However, many job shops cope with thousands of
parts and dozens or hundreds of workcenters. Intuitive and informal methods are insufficient for
these situations.
Production Flow Analysis (PFA) or Coding and Classification (C&C) are often necessary. The
Lean literature sometimes presents simple examples of PFA but these examples are rarely
practical and rarely involve more than a dozen products. Real-life situations are more difficult
and complex. For an example of a real PFA chart developed for an electronics job shop,
click here. Software such as
PFAST may also be useful.
Kanban & Scheduling
Kanban
has limited application for many job shops. The volumes are too low and demand too erratic.
However, there may be opportunities for certain items and careful analysis is prudent.
In addition there may be opportunities to use kanban with purchased parts, hardware items,
accessories or items that are common to multiple products. Kanban and MRP type scheduling can
co-exist in the same workcell.
When deciding on kanban, variability of demand is more important than overall volume. For
example, the demand for an item may be only 2-3 parts per week, but if it is always 2-3 parts
per week, kanban is effective.
|
Value Stream Mapping & Process Mapping
Value Stream Mapping has been a
popular technique but is pretty useless in a job shop situation. It does not fit well when
multiple routings are required and it is too complex.
In theory, we could group parts that are similar and then apply VSM. However, these parts are
likely to have different work times, setup times and inventory levels. Some workcells might have
dozens or even hundreds of different parts. There is simply not enough room on a Value Stream
Map for all this data. Moreover, once you put it on the map there would be too much data to
comprehend and analyze.
Process
mapping is much simpler. It gives a better visual perspective. After Process Mapping, Group
Technology identifies families. The detailed time, capacity and volume analysis is done on
spreadsheets and database tools meant for such complex data.
A generally good approach is the following:
1) Develop 3-4 process maps for typical parts. This shows a good
overview of the processes.
2) Use GT to identify families of parts that match well with potential
workcells.
3) Map the process for each workcell using a typical part within the
family. Use this map as the starting point for cell design.
4) Work out capacity, staffing and lot sizing using a spreadsheet.
Our pages on Workcell Design show how this works
and the author's book, Facilities Planning & Workplace
Design provides steps through the process in detail.
Focused
Factories
A careful analysis of many job shop operations may reveal that they are not pure job shops.
Certain products may have fairly high and/or consistent volumes. Yet, for a variety of reasons,
these high-volume and low-volume products mix together in the same shop, with the same equipment
and the same scheduling.
These situations are ideal for Focused
Factories and Plant-Within-Plant approaches. The split is usually based on volume. One
section of the plant has cells or lines that make a single product or variations of that
product. The other section has GT cells producing a much wider variety. Each section should have
its own scheduling system and chain of command.
Work Standardization
Work standardization in a job shop will typically have much less detail than the
standardization in a higher-volume facility. There are simply too many parts and the volumes are
too low to justify a high level of detailed standardization. Job shops depend on the skills and
knowledge of their workforce.
Implementation
The figure at right shows typical priorities for a job shop. Our pages on
Lean Implementation explain the development of
these priorities, a Lean Strategy and implementation plan.
In high volume operations, cells will be simpler and similar. One or two prototype cells
provide models for the remaining cells. With a job shop each cell may be unique. Moreover, each
cell may have unique scheduling, process and coordination problems that the individual cell
teams must work out for themselves. There is no standard model to copy.
For this reason, a typical job shop implementation is likely to be slower than the
implementation in higher volume plants. Moreover, the job shop will require an extensive GT
analysis prior to cell design in order to sort out part families and cells and this requires
considerable time.
Summary
Job shops really are different. That does not mean that Lean Manufacturing cannot apply. It
only means that an intelligent application based on fundamentals rather than a formula is
necessary. This is true for any plant but more so with a job shop.
References
IRANI, SHAHRUKH A., Handbook of Cellular Manufacturing
Systems, Wiley, New York, 1999.
LEE, QUARTERMAN, Facilities & Workplace Design,
Engineering & Management Press, Norcross, Georgia, 1997.
SURESH, NALLAN C. AND KAY, JOHN M.,Group Technology and
Cellular Manufacturing, Klewer Academic Publishers, Boston, 1998.
KAMRANI, ALI K., PARSAEI, HAMID R. AND LILES, DONALD H.,
Planning Design & Analysis of Cellular Manufacturing Systems, Elsevier, New York, 1995.
WRENNALL, WILLIAM, AND LEE, QUARTERMAN, Handbook of
Commercial and Industrial Facilities Management, McGraw Hill, August, 1993.
|