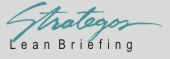
The free newsletter of Lean Manufacturing Strategy
Lean Briefing Archives
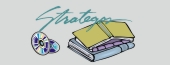
Books & Videos
The Strategos Guide To Value Stream and Process Mapping goes far beyond symbols and arrows. In over 163 pages it tells the reader not only how to do it but what to do with it.
More info...
Strategos Guide to Value Stream & Process Mapping
Also...
Guide to Cycle Counting
Facilities & Workplace Design
Warehouse Planning Guide
Human Side of Lean Video

|
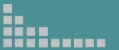 |
How To Chart (Map) Your Process
A Step-By-Step Tutorial
|
Process Mapping is also known as
Process Charting or Flow Charting. It is one of the oldest, simplest and most valuable
techniques for streamlining work. It is also subtle and requires experienced facilitators for
best results. some of the benefits of Process Charting (Mapping) are:
A process map visually depicts the sequence of
events to build a product or produce an outcome. It may include additional information such as
cycle time, inventory, and equipment information.
Several systems of conventions exist. At Strategos,
we find that the original system invented by
Frank Gilbreth in the early 1900's is
still the most useful.
|
The Gilbreth approach is highly visual and
discriminates between waste and value-added activity. It is also simple, intuitive and easily
used by untrained groups. An experienced facilitator, however, is required.
The figure below shows a Process Map example and
instructions for its construction. In most situations only the circle symbol
(Operation) adds value.
-
Follow one product or a
narrow product group.
-
Place the dominant
component on the right.
-
Show other components and
subassemblies on the left.
-
Describe each event
concisely.
-
Add additional information
as required.
-
Merge items on the chart
only when the physical items are merged.
|
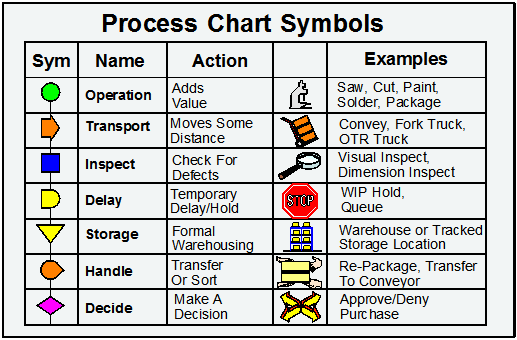 |
General Hints
Identify The Product
Process maps and charts show the sequence of events that act on a product. Therefore, we must
carefully identify the product and ask "What is being done to the product."
In manufacturing processes, the product is physical and easily identified. For service and
office processes it is easy to confuse activity with the product.
|
Information Flows
A common criticism of Process Mapping is that it does not represent information flows. And, many Process Maps do not show information flows, but they can show them and often
should.
To map information, consider it as packet such as a work order or a database record.
Or, a component necessary to complete the event. Chart information
sequence with dashed lines. (Example)
|
The Team
When mapping the current state, assemble a broad based team from all areas and several
levels. It should include workers because they know the details of what really happens. It
should include engineers and support people because they have a broad view of the process and
know what is supposed to happen.
|
Drawing the Working Map
During a mapping session the entire team should see the entire map. And, each
individual be able to focus on any detail that sparks a thought.
Draw the map on large paper sheets. This may cover several
walls in an average conference room. Later the map can be redrawn with computer tools for
distribution. (Example)
|
Using Symbols
Rules of Thumb
These rules of thumb apply to a factory-level maps. You may want to modify them for more
detailed maps.
Storage & Delay--
-
When a product is in an official storage location with a record, use the Storage symbol.
-
If the product is set aside casually to wait for a fork truck, for example, use the Delay
symbol.
-
Set a time, say five minutes, below which a Delay will not be shown.
Handling & Transport
-
If the product moves more than three paces, use the Transport symbol.
-
If the product is sorted, rearranged or moved less than three paces, use the Handling
Symbol.
-
If a
transport delay is more than five minutes for a macro-level map, show it. Otherwise consider
it as part of an adjacent event. Use a 30-second limit for micro-level maps.
When In Doubt...
-
Combine
Symbols.
-
Add a question mark to signify the uncertainty.
|
Value Added
Occasionally, it is unclear whether an event adds value. Here are three useful tests:
The following process events often bring controversy:
Inspection--
-
Inspection refers to an examination of the product to determine if
work has been done correctly. It does not refer to statistical process control activities that lie
outside the chart.
-
Inspection rarely adds value because it does not change the product.
- When the customer perceives inspection as value adding, requires it and pays for
it, you may want to consider it a value adding event.
Curing/Drying--
These change the physical properties of the product and should use the "Operation" symbol
rather than a "Delay" symbol.
Transport--
|
Setups
and Batches
Batch processes and setups frequently confuse mapping teams. When this happens, return to the
question "What is happening to the product?"
Setups
During a setup, nothing happens to the product. It
simply waits for the completion of the setup. This map detail shows a typical batch operation
with setup.
The setup is a separate process and can be studied as such. It has nothing to do with product
other than causing a delay and does not show on the process chart.
Batching
Processing in batches introduces a delay before and after an operation while the remainder of
the batch is processed.
Batching for transport can be as problematic as batching for processing. Moves often have
delays when they wait for material handlers.
|
Detail Levels
Process maps can depict many levels of detail. Like a Mandelbrot set, every event can expand
to reveal more and more detail, as shown in the figure. Determining an appropriate level for the map is vital. With too much detail, the map becomes
too large to see or print; too little and important elements are lost.
The best level depends on your purpose. Here are some guidelines:
Workflow & Group Technology-- The objectives here are to
simplify movement between departments or develop part families. Operation events normally
correspond to operations in the process specification or routings. Often, each operation is in a
separate department. When charting at this level, be sure to include all moves, set downs and
delays between departments as well as any moves from a departmental staging area to the process
equipment.
Workcell Design may require a finer breakdown of the events. Once the product families and
cells are selected, only those events within the cell or immediately subsequent and prior need
be depicted.
Workstation Design-- At this level, events are quite
detailed. In most situations, a process map is not the best way to analyze workstations,
although variations such as right-left hand charts are often useful.
|
Most beginners make their first charts with too little detail and often overlook non-value
added events.
In theory, process mapping could be extended to sub-micro maps that show micro-motions. Or,
It could extend to global value-chain processes. But, usually, other tools are more suitable for
these situations.
The maps below show two levels of detail. The upper map shows individual elements
within a workcell such as Head Subassembly and Body-Coil Subassembly. It also shows the
moves and delays between these elements within the cell.
The lower map explodes the Head Subassembly operation into smaller elements. Even
this map could conceivably be exploded into micro-motions, but there is not much point
in doing so.
At an even higher level than shown below, all assembly operations would compress into
the single element, "Assemble Pump." Such a map would work well in sorting out product
families.
The first map, below, would be appropriate for workcell design while the second map
would help workstation design.
|
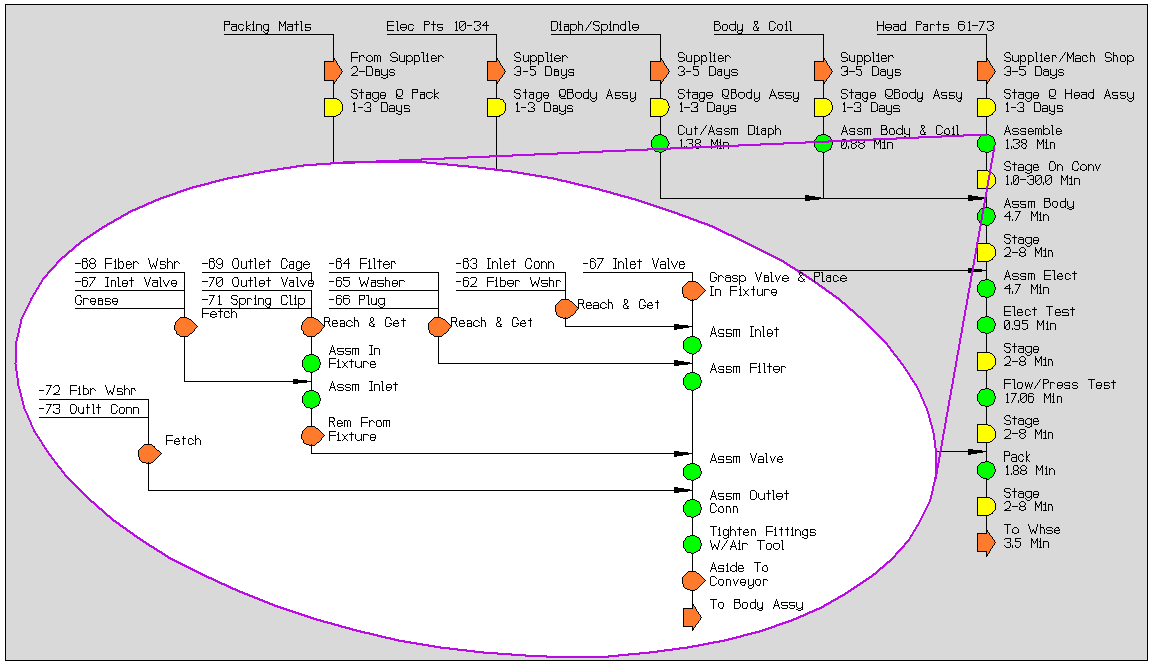
Setting Boundaries
Setting Boundaries
Process maps are most useful at a micro or macro level. Micro level charts show small steps
such as "Assemble Cover" and "Adjust Tension." Their boundaries are usually the physical
boundaries of a workcell or department.
Macro-level maps show the process on a larger scale and often have boundaries corresponding
to the boundaries of the factory. Macro-level maps consolidate small process events into a
single larger event such as "Assemble Product."
|
A road map of Missouri also shows parts of Iowa, Kansas, Illinois and Arkansas. Apply this
idea to your process map also. Start a bit upstream from the perceived area of interest and move
downstream a bit beyond your area of interest.
For example, if you are concerned with the entire factory, start at the supplier's dock or
inbound truck. Include the customer or the outbound truck.
If the project is a workcell design, start with the upstream workcenter or area. In this way,
you capture moves in and out. You may discover that factors outside your perceived area of
interest have major effects.
|
|
|