Setup
reduction should be approached in four phases or stages as illustrated below. It is usually best
to repeat the process through several iterations spaced several months
apart. The initial phases
of setup reduction (SMED) are straightforward and easy, yet often bring the greatest benefits.
People are constantly amazed at how much time is wasted through disorganization and general
messiness.
Improving elements and eliminating adjustments will require more imagination, time and cost.
Even here, the improvements are sometimes astonishingly simple and easy.
The "Kaizen Event" or "Blitz" is an excellent
vehicle for setup reduction. It generates enthusiasm and fast results which make the efforts
less mundane.
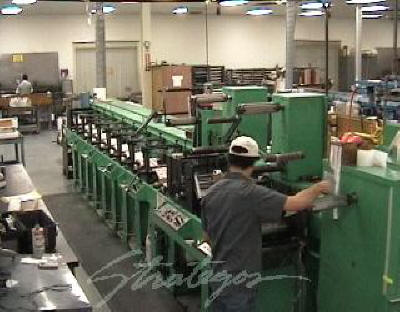
|
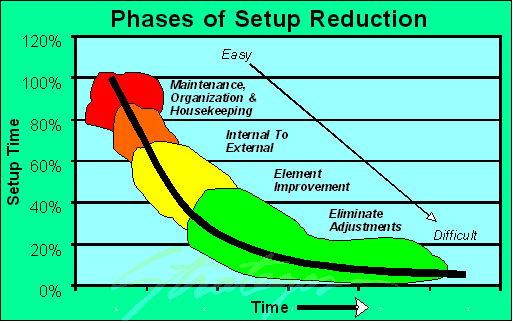
1. Maintenance, Organization and Housekeeping
It often happens that setup problems are related to poor maintenance such as worn parts, worn
tooling, dirt, or damaged threads. Disorganization and poor housekeeping are also contributors
to setup problems. These are easy to fix and should be a first step.
2. Internal Elements to External
Internal elements occur when the machine is down. Examine each internal element and see if it
cannot be done externally. For example, the pre-heating of an injection molding die could be
done before it goes into the machine.
3. Improve Elements
Here we examine every element to see how we can eliminate it, simplify it, reduce the time
required or improve it in some other way.
4. Eliminate Adjustments
Adjustments are often the most time consuming, frustrating and error prone parts of a setup.
There are many ways to eliminate them entirely and this is the ultimate goal.
|