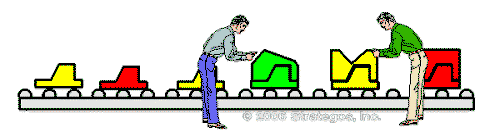
Mixed Model Production--What Is It?
Mixed Model Production is the practice of assembling several distinct models of a product on
the same assembly line without changeovers and then sequencing those models in a way that
smoothens the demand for upstream components.
The objective is to smooth demand on upstream workcenters, manufacturing cells or suppliers
and thereby reduce inventory, eliminate changeovers, improve kanban operation. It also
eliminates difficult assembly line changeovers.
Toyota developed the concept in the 1960's in response to the problems created by line
changeovers. It originally applied to long assembly lines such as those used in automotive.
However, Mixed Model Production is adaptable to other situations. There are also
alternatives, such as assembly cells,
that accomplish the same purpose, often with better results. This topic also relates to
Focused Factories in because it addresses the
same issues at a more detailed level.
The Underlying Principle
Henry Ford demonstrated that steady, repetitive production dramatically reduces cost. This is
true for both assembly operations and for upstream fabrication. However, when final assembly
models proliferate and the issue is addressed by changeovers and long runs on the assembly line,
it creates highly variable demand in upstream fabrication and subassembly.
|
In
A Nutshell
Definition &
principles behind Mixed Model Production.
|
Ideal Workflow
The ideal production system would be like a smoothly flowing stream with many tributaries and
no pools, dams or other accumulations.
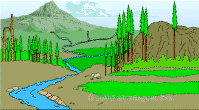
Or...
...like a marching band with everyone in step, spaced at a fixed distance, all in time to the
music beat and smoothly flowing from one figure to another throughout the performance. This is
the origin of "Takt Time."
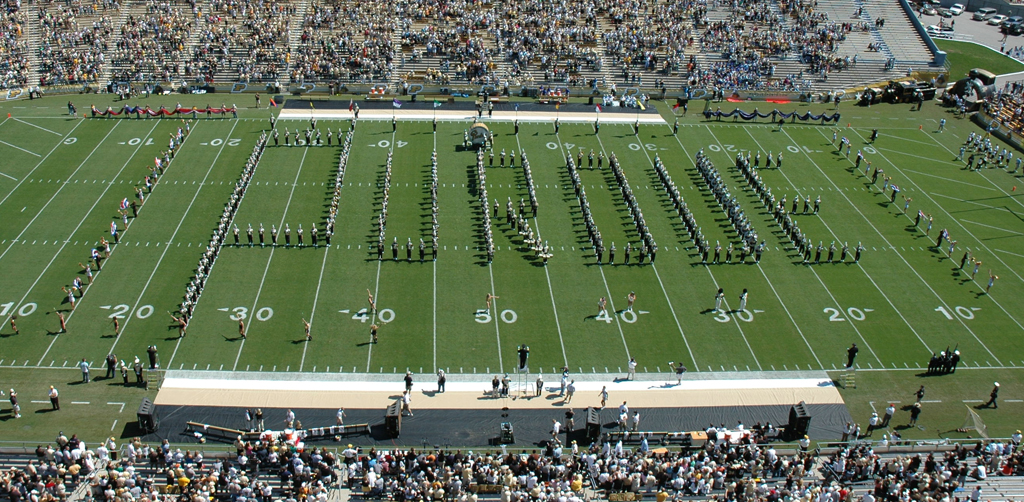

|