Using The Mental Model
First, imagine the ultimate factory as shown above with your products and customers. Then ask the following questions:
What would be the characteristics of the equipment, people and layout in this factory?
What must be true for this to be possible?
What are the root causes for inventory in our plant?
An Example
In many factories a primary
"reason for
inventory" involves intertwined issues of equipment scale, setup, batching,
and workflow. The causal diagram (below) illustrates.
The problem starts with equipment that is larger and faster than required for
a single product. This causes multiple products to run on the same equipment.
Two effects ensue:
1) Changeovers become necessary.
2) Different products follow different routes.
In addition, large-scale equipment often requires difficult and
time-consuming setups. The combination of changeover and long setup forces large
batches that promote high inventory. Different routes force functional layouts
with complex flows that also increase inventory.
High inventory brings all sorts of waste in material handling, space and
quality (not shown). This diagram is over-simplified. In reality, it has multiple, subtle reinforcing loops that exacerbate the
problem over time.
At Toyota, Shingo attacked both root causes. First, he developed the SMED system that reduced
changeover times and, thus, batch sizes and inventory. Second, he scaled down the equipment, where possible, thus enabling Cellular
Manufacturing and its simplified workflow.
SMED and workcells did not become part
of the Toyota Production System because they had some sort of cosmic virtue. They were employed because they reduced inventory and waste in the Toyota context.
|
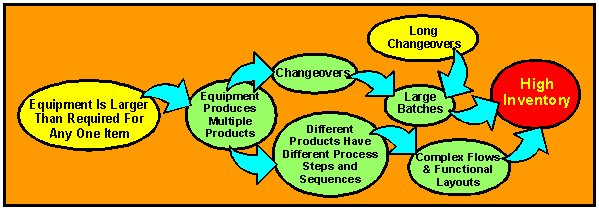
Causal Diagram for Setup Reduction
(SMED)
The arrows in this diagram indicate influences.
This particular diagram shows that one cause of high inventory is the selection of large
equipment that must run many products.
|
The Key Point
Systems Thinking visualizes causes and effects,
interactions and dynamic behaviors. Both Systems Thinking and Lateral Thinking are important
when developing a Lean Manufacturing Strategy for your particular plant. This is where
leadership plays a key role.
Our Mental Model is simple; the implications profound.
It led Toyota to setup reduction, workcells and, eventually, the other tools of Lean
Manufacturing. In other situations, it may lead to a somewhat different set of tools.
The moral:
-
Do not copy Toyota's tools and techniques blindly; they are not universal.
Use Toyota's Mental Model, it is universal.
Our additional pages detail procedures for developing your own Strategy and implementation plan.
|