PDF brochure (You need ACROBAT READER -
download
program)
Turning
The values shown below apply to tough grades of sintered carbide, which
are unavoidable for those operations where the material might be
subjected to impacts, such as when turning steel with flame-cut edges.
Carbide class |
Formulae: |
Feed speed |
= cutting speed = workpiece
diameter
= speed (rpm)
= 3.14
= feed rate
= feed rate (mm/rev) |
With higher feed rate reduce cutting
speed. |
|
Countersinking and counterboring
For spot-facing and countersinking are best used tools with replaceable
blades made of sintered carbide and with a rotating guiding shaft. Use
cooling fluid.
Counterboring bit with replaceable blades and rotating guiding
pivot |
Countersinking bit with replaceable blades and rotating guiding
pivot |
Feed rate f (mm/rev) |
Speed n (rpm) |
1. if chips are
breaking off, feed in 2 mm steps
2. if the machine performance is
low, select cutting speed in the lower part of the value range
|
For WELDOX material shown in the table can be used HSS countersinking
machines with three blades and a guiding pivot. It is necessary to
supply enough cooling fluid.
Cutting threads
Provided you have selected the right tap, you can cut threads to any
types of HARDOX and WELDOX products. We recommend to use taps with four
grooves which can withstand greater torques, which are when cutting
threads in hard materials unavoidable. When cutting threads in HARDOX
and WELDOX, we recommend to use as a lubricant oil or thread cutting
paste. For softer WELDOX 420, WELDOX 460 and WELDOX 500 steel can be
also used emulsion.
In applications where the thread strength is not critical, a bigger hole
than a standard size can drilled (by approx. 3%), which will reduce the
tension during the thread cutting and hence prolong the thread's life.
This applies particularly when cutting threads in HARDOX and WELDOX 1100
steel.
Milling
SELECTING TOOL AND MILLING METHOD
To guarantee rational production, we recommend to
use milling tools with sintered carbide cutting tips.
Face milling
Milling with rectangular tips
Cylindrical face milling |
Roughing |
Finishing |
Select tool with set 90° angle |
Less stable tool |
Stable tool |
Select tool with round tips -particularly when
machining HARDOX |
Select toolwith 45° angle |
|
Select coated cylindrical face tool HSS-Co |
Select cylindrical face tool CC with full-carbon
blades or with inserted rotary blades |
*) do not use cylindrical face tool HSS when machining flame-cut edges
When milling, the following recommendations should be followed:
- Check whether the workpiece is properly clamped.
- If the machine performance is low, use a milling tool with courser
teeth
- If possible, do not use a universal tool, as this will weaken the
tool's fitting and reduce the transfer of power.
- The cut width should be roughly 75 - 80% of the milling tool's
diameter (see values on the right).
- When the surface being milled is narrower than the milling tool's
diameter, the tool should be positioned eccentrically in such a way that
as many teeth as possible are cutting.
- When milling flame-cut edges, the minimum cutting thickness should be 2
mm, to avoid the strengthened layer on the flame-cut edge (see the
graph).
|
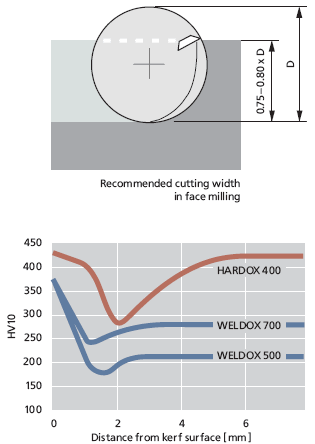 |
Drilling
Drilling can be done using high-speed steel or sintered carbide bits.
The type of bit to be used depends on the drill available and its
stability. Regardless what drilling machine is used, it is necessary to
minimise vibrations.
Rotary or percussion drilling machines
In order to reduce vibrations and increase the drilling machine's life,
we recommend:
- to maintain the shortest possible distance between the bit and the
stand
- not to use wooden pads
- to clamp the workpiece properly and drill as close to the pads as
possible
- use a short spindle and a short drill bit to allow shortest possible
distance between the bit tip and the arm.
- just before the drill bit gets through the material, release for about
a second the feed. Otherwise the tip of the drill bit might due to
backlash and elasticity break off. When the backlash and elasticity
disappear, you can resume the feed.
- Make sure that the supply of cooling fluid is adequate
Single holes can be drilled using an
ordinary HSS drill bit. To guarantee rational production, we recommend
to use drill bits made of micro-alloy fast-cutting steel (HSS-E) of
fast-cutting steel with cobalt (HSS-Co). |
|
Use HSS-Co drill bit (with 8% cobalt) with a gentle
pitch and a robust core which will withstand high torques. |
More stable machines such as for example vertical turret
lathes and fixed bed milling machines:
In order to increase productivity, make use of the benefits offered by
sintered carbide drill bits in state-of-the-art and stable machines.
You can choose from three main types of sintered carbide drill bits. The
choice will depend on the machine's stability, workpiece clamping, the
hole diameter and the required tolerance. Always use the shortest
possible drill bit.
Cooling fluid:
- Use cooling fluid for drilling.
- The rule for drilling with internal supply of cooling fluid: cooling
fluid flow [l/min] = drill bit diameter [mm].
Full-carbide drill bit
- diameter from ca 3 mm
- small tolerances (high precision)
- can be ground
- sensitive to vibrations
Drill bit with brazed carbide blades
- diameter from ca 10 mm
- small tolerances (high precision)
- can be ground
- less sensitive to vibrations as full-carbide bit
Drill bit with rotating inserted blades
- diameter from ca 12 mm
- high productivity
- bigger tolerances than the other types (lower precision)
- less sensitive to vibrations as full-carbide bit
|
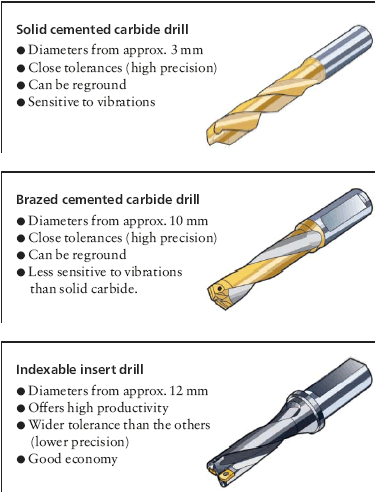
|
Cutting
speed vc (mm/min) and feed rate f (mm/rev)