Beginning
in the 1950's with early missile programs, the Department Of Defense sponsored a new science
called Reliability. Reliability is the science of maintenance. It uses statistics and failure
theory to measure, understand and improve the performance of equipment and maintenance.
Reliability theory can guide engineers as they design and test new equipment. After equipment
has been in service, reliability data tells the maintenance engineer how to improve its
performance.
As the Gulf Wars demonstrated, this science has produced outstanding results in defense.
Regrettably, little of this knowledge has found its way into industry. Most maintenance
operations still operate on the principal of "if it ain't broke, don't fix it". This breakdown
theory of maintenance generates several undesirable effects:
Breakdowns occur at the worst moment-- when a customer is waiting, process timing is
important, or when people are standing by. This unplanned downtime is far worse than intended
downtime. Breakdowns often cause collateral damage that far exceeds the original problem. For
example, a $38.00 roller bearing on a plastics extruder fails. The resulting misalignment of the
shaft destroys the gears and the pinion shaft, three other bearings and an oil seal. The sudden
stoppage causes plastic to freeze in the barrels. The total cost is about $13,000 plus three
days of lost production. A routine inspection using vibration analysis or even the touch and
hearing of an experienced mechanic could have prevented almost all of this loss.
Breakdowns are one of many reasons for excessive inventory buffers. Such inventory allows
other production to proceed while the breakdown is fixed. But this inventory is expensive.
Moreover, there are other associated costs such as space, tracking and insurance. At least 75%
of quality problems have a maintenance component. This causes customer dissatisfaction, scrap
and further bloats inventory.
Phantom capacity, the difference between theoretical capacity and actual output is often the
result of maintenance problems which generate downtime, scrap and scheduling difficulty. Some
plants have as much as 40% phantom capacity.
The True Cost Of Maintenance
Accounting systems rigorously capture the direct cost of maintenance. They rarely capture the
costs of non-maintenance such as those above. The graph shows how total cost varies with the
level of maintenance. The left side of the curve reflects a "breakdown" maintenance strategy,
i.e., maintenance effort is assigned only when equipment fails. As the level of maintenance
moves up, effort is made to regularly service equipment.
The Five stages of maintenance
1- No action until equipment
fails
2- Routine service-- oil and
grease
3- Inspection and preventive
repair
4- Equipment Re-Engineering
5- Predictive Maintenance
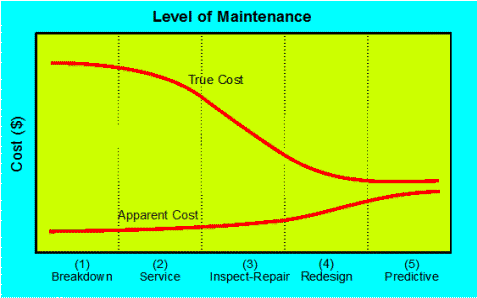
|
Metrics
The key to excellence in maintenance is a good system of
metrics. Some of the key metrics are:
-
Availability
-
Mean Time Between Failures (MTBF)
-
Mean Time To Repair (MTTR)
-
Mission Reliability
-
Breakdown Effort Ratio
-
Maintenance Cost/Output Unit
Total Quality Management (TQM)
Quality teams will find many issues that involve
maintenance. The technical tools such as Pareto Diagrams, Ishikawa Diagrams and control charts
are valuable diagnostics and indicators. Combined with the metrics and tools of Reliability they
help the maintenance department permanently solve problems.
Teams
Initially, maintenance personnel should be members of
problem-solving teams. When the company has fully re-structured, these people may become part of
Self-Directed Work Teams. Maintenance will also form internal teams to examine their internal
processes as well as specific equipment problems where maintenance issues dominate.
Organization Restructuring
As the above elements come into place, the maintenance
organization should change. More maintenance tasks are taken on by the operators and users of
equipment. The centralized maintenance department takes on a new mission which emphasizes:
-
Specialized expertise that does not fit
easily into operating units
-
Setting minimum standards for metrics and
reporting
-
Training
-
Common Spare Parts Stocking
Information Technology
Information Technology has made rigorous use of
maintenance metrics easy. Many maintenance software systems exist. They can assist in almost
every area of maintenance. The track spare parts, compile time and costs, track metrics,
schedule work and analyze vibration. But a software program does not guarantee good maintenance
performance. Software cannot compensate for a lack of fundamental knowledge. In many cases,
software has harmed maintenance efforts by diverting resources and delaying action on the true
causes of non-performance.
What You Can Achieve
Competitiveness and Profitability are the goals of our
work. Maintenance can and should be a prime contributor. We can help you select the appropriate
elements from TQM, BPR and other innovative programs and successfully implement them in your
operations. A well executed drive towards maintenance excellence can:
-
Achieve Availabilities Of 90%-98%
-
Reduce Failure Rate 50%-90%
-
Increase Capacity 10%-30%
-
Improve Quality
-
Reduce Frustration
|