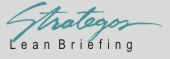
The free newsletter of Lean Manufacturing Strategy
Lean Briefing Archives
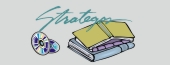
Books & Videos
The Strategos Guide To Value Stream and Process Mapping goes far beyond symbols and arrows. In over 163 pages it tells the reader not only how to do it but what to do with it.
More info...
Strategos Guide to Value Stream & Process Mapping
Also...
Guide to Cycle Counting
Facilities & Workplace Design
Warehouse Planning Guide
Human Side of Lean Video

|
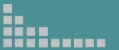 |
Benefits From Lean and Cellular Manufacturing
What You Can Expect From Lean Manufacturing Strategy
|
|
General
Lean Manufacturing and Cellular Manufacturing offer many advantages in material handling, inventory,
quality, scheduling, personnel and customer satisfaction. Workcells derive these advantages from their small size and process integration. They also fit the human penchant for working in small
groups. The links below summarize the benefits you can expect from a well-managed design and implementation.
|
|
|
Inventory & Scheduling Benefits
Lean manufacturing
benefits extend to inventory, scheduling and production control. The functional layout presents
severe scheduling and inventory control difficulties. Cellular layouts, a feature of Lean
Manufacturing, simplify the underlying
process and thereby simplify scheduling.
Every
inter-departmental move requires an outbound queue and an inbound queue. Such queues tend to be
quite large because it is difficult to precisely time the completion of each operation and
coordinate the subsequent move. Cellular operations dramatically reduce material movement. This
consequently reduces the number of queues and the inventory in each queue.
Lot
sizes tend to be larger in a functional environment. This partly results from the complexity of
scheduling. It seems easier to schedule a small number of large lots rather than a large number
of small lots. Equipment selection also plays a role. Functional layouts lend themselves to
large-scale equipment. Such equipment processes a wide range of products and increases the
volume for a given process. Large-scale equipment also tends to reduce direct labor and appears
to be more efficient. But large-scale equipment is often difficult to setup. It must address a
wider range of products. Expensive, large-scale equipment requires high utilization. High
utilization requires more inventory.
Element |
Functional |
Cellular |
Improvement |
Lot Sizes |
Large |
Small |
50%-100% |
Queues |
12-30 |
3-5 |
50%-80% |
Stocking Policy |
Make-To -Stock |
Make-To-Order |
Eliminate FG Stock |
Inventory Turns |
3-10 |
15-60 |
60%-90% |
Throughput |
Weeks |
Hours |
50%-90% |
Equipment Utilization |
40%-100% |
20%-80% |
Functional Utilization Often Unrealized |
Scheduling |
Complex (MRP) |
Simple (Kanban) |
Much Easier |
|
Average throughput
time is directly proportional to inventory. We refer to this relationship as Little's Law. When
inventories shrink in a cellular environment, average throughput time shrinks proportionately.
The reduction in inventory frees up capital and space for more worthwhile investment. The
improved throughput time improves customer response and helps stabilize the system.Duplication
of equipment in cells seems to cause low utilization. Several factors can mitigate this:
-
The wide variation in production requirements that characterizes functional arrangements
often results in lower utilization than one would otherwise expect.
-
Workcells typically produce only a limited number of products out of the factory's product
mix. They therefore need smaller-scale, lower-volume equipment.
-
Cellular equipment is often simpler, and less expensive than corresponding equipment in a
functional arrangement. Therefore, low utilization in a cell is less important.
-
The capital freed by inventory reductions usually provides more than enough money for
additional equipment. In effect, workcells trade inventory for excess capacity. This
tradeoff is usually quite favorable.
-
Cells may share equipment and thereby reduce
duplication. Certain operations can remain
centralized.
-
The designer can often build workcells around specific pieces of large-scale, expensive
equipment. Duplication is then reserved for low-cost equipment in secondary operations.
Functional layouts usually require the capabilities of Materials Requirements Planning (MRP)
systems. These systems are complex, expensive, and cumbersome. A
cellular layout allows
simpler scheduling approaches such as kanban and broadcast.
|
|
Material Handling Benefits
Lean manufacturing benefits include those from material handling. The illustrations of a functional
and cellular layout vividly demonstrate many of these material handling benefits. Fewer moves,
shorter travel distances, and simpler route structures add up to impressive savings. These
characteristics also contribute to savings in inventory, coordination and quality.
The product-focused cellular layout has fewer interdepartmental moves compared to a functional
equivalent. This reduces handling frequency and cost by as much as 90%. The cellular layout also
reduces the queuing, delays, tracking effort, and confusion that accompany material
movement. Travel distances are shorter in the cellular layout. In addition to reducing the cost
of long moves, this improves communication and often enables visual control
systems. Complex
routings are characteristic of functional layouts. Many products and components visit multiple
work centers in multiple sequences. This, in turn, necessitates complex process plans and
extensive documentation. Cellular routings are simple.
|
Functional layouts have variable route structures since many products move in so many
different directions. This necessitates costly handling devices such as fork trucks or Automated
Guided Vehicles that can accommodate such variable route structures. The cellular layout, by
contrast, has simpler and more stable route structures that may allow simple and cheap handling
devices such as conveyors and chutes.
Element |
Functional |
Cellular |
Improvement |
Inter-department Moves |
Many |
Few |
50%-90% |
Travel Distance |
500'-4000' |
100'-400' |
70%-90% |
Routings |
Complex |
Simple |
Possible Automation |
Route Structure |
Variable |
Fixed |
Simplified |
|
|
Quality Benefits
Functional layouts require the product to move many times between departments with a separate
operation at each department. When the product is defective, it is often difficult to pinpoint
where the defect has occurred. In a cell, most or all operations occur in one area and among a
small team. This focuses responsibility and motivates the team to avoid similar defects in the
future.
While Statistical
Process Control techniques can improve functional operations, they are easier to apply and more
effective in practice with a workcell environment. Most functional layouts use a sort of
"Quality Police", the Quality Control Inspectors, to enforce quality. With teams and workcells,
quality is more likely to be self-enforced.
Feedback on
quality problems is faster and surer in a cell than it is in a functional arrangement. This is
because the various processes and people are very close, usually within conversational range.
Since teams are often used within cells, team spirit motivates quality improvements.
|
Because the
operations in a functional layout are scattered, problem solving that cuts across departmental
boundaries is difficult. Departmental loyalties work against it. The coordination of information
from many sources works against it. Forming an effective problem-solving group is problematic.
Cellular environments generally have a functioning work team. When this team switches to a
problem-solving mode, the team is immediately effective.
Element |
Functional |
Cellular |
Improvement |
Responsibility |
Fragmented |
Focused In Cell |
50%-90% Improvement |
Approach |
Police Action |
Self-Enforced |
Happier Teams |
Motivation |
Avoid Punishment |
Pride |
Peak Performance |
Problem Solving |
Difficult & Fragmented |
Team-Based |
Permanent Solutions |
|
|
People Benefits
In
times past, manufacturers could ignore the psychological needs of their employees. Labor was
cheap and employees were concerned with survival in a world of scarcity. The paycheck meant
everything. Now, "The Greatest Generation" has given way to "Generation X" and much has changed.
The volume and
complexity of information flow in any manufacturing plant is enormous. Functional arrangements
increase this volume and complexity by orders of magnitude when compared to cellular
arrangements. This is partly because cellular arrangements are simpler, and less information is
required. In addition, since workcells are more self-contained, much information flow is within
the cell. Transfer of information is quick, simple and informal. Information is often obvious
from visual observation and available to all.
For a various
reasons, functional layouts inhibit teamwork while cellular arrangements enhance, even demand
it. Functional layouts scatter the people who work on a given product. Cellular layouts bring
people together. Workcells require teamwork to function effectively; functional layouts do not.
Functional layouts are often dysfunctional regardless of the level of teamwork.
In a functional
layout, products are difficult to see and identify. Since the skill range is narrow, workers may
become "button-pushers." People have little sense of accomplishment because they cannot see the
results of their efforts.
|
A workcell
requires a broader range of skills. These include not only job skills, but interpersonal skills.
As a result, cellular workers are more involved and take greater responsibility for their work.
Cellular manufacturing takes advantage of human flexibility and knowledge while meeting many
psychological needs. Satisfying psychological needs is the key to motivating today's workforce.
Element |
Functional |
Cellular |
Improvement |
Communication |
Slow & Uncertain |
Fast & Positive |
Quality & Coordination |
Teamwork |
Inhibited |
Enhanced |
Effective Teams |
Motivation |
Negative, Extrinsic |
Positive, Intrinsic |
Strong Motivation |
Skill Range |
Narrow |
Broad |
Job Enrichment |
Supervision |
Difficult & Fragmented |
Easy & Localized |
Fewer Supervisors |
People in
functional environments often derive motivation only from their paychecks. Such motivation is
"extrinsic" and brings minimal compliance with job requirements. Cellular layouts depend on
"higher" motivations such as pride in the team and feelings of accomplishment. Such motivation
is necessary for superior performance.
Supervisors in a
functional layout spend most of their time on coordination. With lean, coordination is simple.
Most coordination is informal, fast and without disconnects.
|
|
What The Customer Sees
The customer sees improved quality and this is an obvious benefit to both customer and supplier.
Customers see faster response to unusual requests for customized products or expedited delivery.
They see faster and more reliable average deliveries that make their tasks easier. Cellular
manufacturing allows manufacturers to deliver small quantities reliably without holding large
inventories. The inherent quality improvements in a cellular layout also find their way to
appreciative customers.
Element |
Functional |
Cellular |
Improvement |
Response |
Weeks |
Hours |
70%-90% |
Customization |
Difficult |
Easy |
Competitive Advantage |
Delivery Speed |
Weeks-Months |
Days |
70%-90% |
Delivery Reliability |
Erratic |
Consistent & High |
Up To 90% |
Delivery Quantities |
Large Shipments |
JIT As Required |
Locks In JIT Customers |
Quality |
Erratic |
Consistent & High |
Delighted Customers |
|
When suppliers implement Lean Manufacturing, customer response is often the most obvious
improvement. Response refers to the time required for the manufacturer to react to customer
needs.
Fast, reliable deliveries are a hallmark of cellular manufacturing. This is because the
reduction of queues and inventory speed products and components through the system. When fast
delivery is a requirement for a given market, fast throughput or an extensive finished goods
stock are the only options.
In some markets, fast delivery is not important, but reliable delivery is. This means that the
manufacturer delivers the product when it says it will deliver.
As an example, a manufacturer of large power transformers was in a market where new substations
are planned years ahead. The customers have many months to order their transformers. Once on
order, however, it is crucial that the transformer is delivered at the appointed time. If the
transformer is not delivered on the scheduled date, construction crews wait and the project must
be re-scheduled.
Functional
layouts tend to require large lots and infrequent deliveries or they require extensive finished
goods inventories. With cellular layouts, it is easier and less costly to manufacture in small,
frequent lots. This usually matches customer needs more closely.
|
|
|