The "Kaizen Blitz"
or "Kaizen Event" is the fast, big and dramatic
form of improvement. Norman Bodek is introducing us to a sort of "Mini Kaizen" which he calls
"Quick & Easy Kaizen."
Quick and Easy Kaizen recognizes that the person doing a job is the best expert on that
job. It encourages everyone to make small improvements that are within their power to
implement. Over time, these thousands of small improvements have major effects.
Small-scale improvements are easier and faster. The risks are low because they generally have
limited effect. However, the accumulated affect is often greater than a single large
improvement.
Key Characteristics
The Quick & Easy Process
Here is the sequence of events for a Quick & Easy Kaizen:
-
An employee identifies a problem, waste, defect or something not working. He/she
writes it down.
-
Employee later develops an improvement idea and goes to immediate supervisor.
-
Supervisor reviews it and encourages immediate action.
-
The idea is implemented.
-
The idea is written up on a simple form in less than three minutes.
-
Supervisor posts the form to stimulate others and recognize the accomplishment.
|
Quick and Easy Kaizen Benefits
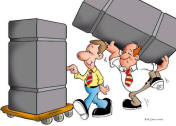
Small Improvements Add Up
|
Mini kaizen empowers employees, enriches the work experience and brings out the best in
every person. It Improves quality, safety, cost structures, environments, throughput and
customer service.
Dana Corporation has used Quick and Easy Kaizen for the past ten years. They get 24 ideas per
month from each employee and 80% have been implemented.
After a workshop, Technicolor in Detroit went from 40 suggestions in July to 550 in October.
Most have been implemented.
Kaizen in The Manufacturing Strategy
Quick and Easy Kaizen is the missing ingredient in many Lean Manufacturing initiatives but is
the heart of the Toyota production system. Toyota states:
"...based on the concept of continuous improvement, or kaizen, every Toyota team
member is empowered with the ability to improve their work environment. This includes everything
from quality and safety to the environment and productivity. Improvements and suggestions by
team members are the cornerstone of Toyota's success."
Mini Kaizen is very much a part of corporate culture. It requires both conscious and
sub-conscious thinking about improvements day by day and minute by minute from everyone.
While each improvement is indeed "Quick & Easy", nurturing such a program and effectively
integrating into corporate culture is far more difficult than a blitz. But, as Toyota has
demonstrated, it offers a more sustained competitive advantage.
|