Introduction
The Human Side of Lean Manufacturing refers to those elements of lean and corporate culture
that impact people's attitudes, their interactions with others and their interaction with the
technical processes. It is important because people are part of the system and part of the
process.
It has taken well over twenty-five years for Lean Manufacturing to have significant impact in
the United States. Even today, it can be argued that most manufacturers talk big but implement
poorly. More than anything else, problems on the Human Side are responsible for this tardiness.
Difficulties With The Human Side
One difficulty in discussing the Human Side is that it permeates every other aspect of lean,
often in subtle ways. It cannot be isolated and addressed as a separate issue.
Kanban, for example seems to be a simple, mechanistic
arrangement of stockpoints, cards and rules. However, when employed effectively, kanban
positively influences teamwork, setup reduction, quality and other areas of process improvement.
These areas, in turn, can make or break the kanban system.
Another difficulty involves the difference between "influence"
and "cause." "Cause" means
that action A always results in effect B. Influence means that action A enhances or increases
the probability of effect B provided that other actions C, D and F also occur with proper
proportion and timing. However, result B, still, may or may not occur. We often prefer to think
about causes rather than influences.
-
Causes are clean, precise, predictable;
-
influences are messy, probabilistic, uncertain and conditional.
History of The Human Side
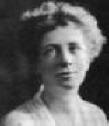
Lillian Gilbreth
Industrial engineer, Wife and partner of Frank Gilbreth.
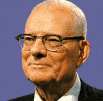
W. Edwards Deming
|
Great leaders from the dawn of history understood it the human side, at least intuitively. In the narrower field of manufacturing, the formal exposition of such concepts dates back at
least as far as Lillian Gilbreth in
the 1920's as well as the
Hawthorne experiments. Eric Trist developed Socio
Technical Systems in the early 1950's.
Of W. Edward Deming's famous
Fourteen Points, at least eleven related to the Human Side.
Then there was Abraham Maslow,
Douglas McGregor and many
others who contributed over the decades. Most of this early work had little impact outside the
classrooms of business schools.
The early Japanese literature on Just-In-Time and Toyota from the 1970's & 1980's emphasized
the human side of the system as one of two underlying themes:
1) Eliminating Waste
2) Respect for People.
For a variety of reasons, the "respect for people" aspect of TPS was mostly lost in
transference to the West. Actually, much of the systemic nature of TPS was also lost in the
translation. Early efforts at applying TPS principles, for example, sometimes focused on "kanban
cards" or "Quality Circles" as The Answer with little consideration for SMED, workcells or
anything else.
In the case of Taiichi Ohno, emphasis on the human
side holds some irony. Ohno was not usually considered a "people person." He was, however,
pragmatic. If "respect for people" was necessary for Toyota's success, he was willing to go
along. For Shigeo Shingo, the human side seemed to come
more naturally. Our article summarizing Spear and Kent's paper, "Decoding
The DNA of the Toyota Production System," shows how the underlying
corporate culture plays
into Toyota's success.
Socio Technical Systems
Eric Trist's work on Socio Technical Systems (STS)
provides a framework for understanding the relationships between the technical and human
aspects of Lean Manufacturing. STS views a factory as an interlocking system of causes,
influences and effects. Some of which are primarily technical (e.g., plant layout) and others
primarily socio or human (e.g.,communication, loyalties or objectives).
Our page on Socio Technical Systems introduces the
concept. A subsequent page condenses the concept into
Principles Of Socio Technical Design. Further pages show how the principles apply to the
conversion of an assembly line to Cellular
Manufacturing and the conversion of a
functional layout to a cellular layout.
|
 
Examples From The Human Side
Many pages on our site
illustrate how the Human Side influences success on the technical side and vice versa.
Here are some of them:
Our video,
"The Human Side of Lean Manufacturing,"
dramatically shows the interaction of workcell arrangements (Technical) and people
(Socio). In this video, workers describe how they designed, built and operate their own
workcell. They discuss the changes it has brought to their attitudes, relationships and
quality of work life.
Socio Technical Systems- Summarizes Eric
Trist's work from the 1950's and condenses it into Principles
of Socio Technical Systems design.
Decoding The DNA of the Toyota
Production System- Summary of Kent & Spear's classic paper on Toyota's culture and
how it views work as an ongoing experiment in process improvement.
Jidoka- This story, related by Taiichi Ohno, shows
how seemingly minor differences in attitude between two supervisors produced
dramatically different results.
The Psychology of SPC shows how Statistical
Process Control (technical) produced behavioral changes (socio) that dramatically
improved quality in a simple assembly process.
Setup Reduction- The graphic on this page
illustrates the chain of influences and causal factors involved in large lot sizes. Note
that most of the links reflect the attitudes of people (socio) that result in large lots
(technical).
The Virtuous Circle of Teams- illustrates how
team training leads to process improvements (technical) that influence attitudinal and
behavioral changes (socio) that further enhance performance.
The Power of Teams- Extensive series of articles
on teams and team development.
Tales From Twelve O'clock High- Excellent
article on leadership illustrated through the classic film "Twelve O'clock High." The
film illustrates how leadership (socio) affects combat operations (technical) in the
form of aircraft availability, bombing accuracy and losses.
 
|
References
SPEAR, Steven and BOWEN, H. Kent, "Decoding the DNA of the Toyota
Production System.",Harvard Business Review, September-October, 1999.
DAVIS, Stanley M., Managing Corporate Culture, Ballinger Publishing,
Cambridge, Massachusetts, 1984.
 
A Personal Note
When
I studied Mechanical Engineering at Purdue University, equations predicted outcomes;
Steel and aluminum were stable; Newton's simple laws explained everything; the vagaries
of people seemed irrelevant.
My simple
little world has changed. People, it seems, are important. Hope, fear, expectation and
intention is now part of engineering. Even physics has changed with the advent of Chaos
Theory and the ever deeper implications of Quantum Mechanics.
Ignoring
these realities only invites trouble or failure . Our best hope is to understand,
however imperfectly, and use that understanding to design effective factories and
processes.
Quarterman Lee
 
|
|