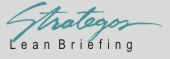
The free newsletter of Lean Manufacturing Strategy
Lean Briefing Archives
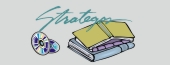
Books & Videos
The Strategos Guide To Value Stream and Process Mapping goes far beyond symbols and arrows. In over 163 pages it tells the reader not only how to do it but what to do with it.
More info...
Strategos Guide to Value Stream & Process Mapping
Also...
Guide to Cycle Counting
Facilities & Workplace Design
Warehouse Planning Guide
Human Side of Lean Video

|
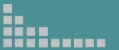 |
Warehouse & Wholesale Inventory Turnover Data
How Much Inventory should You Have?
|
Benchmarking & Monitoring
For most wholesalers and distributors, inventory and the space to store it is the largest
single cost of doing business. From purely a cost viewpoint, less inventory means less cost. At
the same time, insufficient inventory can lead to stockouts, lost sales and unhappy customers.
Balancing these two factors is critical to profitability and growth but achieving that balance
is not obvious or easy.
One metric for evaluating the amount of your inventory is Inventory Turnover. Turnover
measures the efficiency of inventory usage and compensates for differences in sales volume. This
metric is simple, intuitive and easy to calculate. Both sales and inventory value are measured
in terms of Cost of Goods:
|
Turnover can monitor trends or changes from previous periods. It is also useful for
benchmarking against similar firms. When benchmarking with industry averages there are several
cautionary notes:
1) There are wide variations in turnover even within an industry or industry sub-group. The
best firms may have turnovers that are 200%-400% of the industry average. Targeting the industry
average turnover is setting up mediocrity as a goal.
2) There MAY be special circumstances that dictate an average or below average turnover.
However, such circumstances can often be overcome. When low turnover occurs, it is important to
find and rectify the source of high inventory.
Summary data for wholesale industry turnover averages are shown at right. We offer a much
more detailed spreadsheet with over 260 categories and sub-categories for only $6.00.
Click Here to purchase.
|
More than 260 categories and sub-categories
in NAIC code 42. Handy Excel format. Immediate download. $8.00
|
|
Industry Average Inventory Turns |
|
|
Merchant Wholesalers |
|
NAIC |
Description |
Sales (COGS) |
Year-end Inventory (COG) |
Annual Turns |
|
Merchant wholesalers (All) |
1,825,205,737 |
230,839,579 |
7.9 |
421 |
Wholesale trade, durable goods |
909,068,358 |
146,224,425 |
6.2 |
4211 |
Motor vehicle & vehicle parts & supply |
135,856,383 |
17,086,156 |
8.0 |
4212 |
Furniture & home furnishings whsle |
26,309,746 |
5,138,286 |
5.1 |
4213 |
Lumber & other construction matls whsle |
49,362,765 |
5,555,412 |
8.9 |
4214 |
Professional & commercial equipt-supply |
177,110,037 |
20,505,089 |
8.6 |
4215 |
Metal & mineral (except petroleum) whsle |
73,235,527 |
11,965,871 |
6.1 |
4216 |
Electrical goods whsle |
133,707,986 |
18,711,743 |
7.1 |
4217 |
Hardware/plumbing/heating equipt & supply |
41,156,615 |
9,185,806 |
4.5 |
4218 |
Mach, equipt, & supply whsle |
157,129,086 |
41,093,543 |
3.8 |
4219 |
Miscellaneous durable goods whsle |
115,200,213 |
16,982,519 |
6.8 |
422 |
Wholesale trade, nondurable goods |
916,137,379 |
84,615,154 |
10.8 |
4221 |
Paper & paper product whsle |
51,792,304 |
5,117,298 |
10.1 |
4222 |
Drugs, & druggists sundries whsle |
88,808,181 |
12,946,620 |
6.9 |
4223 |
Apparel, piece goods, & notions whsle |
58,866,579 |
12,038,566 |
4.9 |
4224 |
Grocery & related products whsle |
277,515,940 |
17,736,637 |
15.6 |
4225 |
Farm-product raw matl whsle |
118,732,968 |
9,664,441 |
12.3 |
4226 |
Chemical & allied products whsle |
41,394,863 |
4,470,487 |
9.3 |
4227 |
Petroleum & petroleum products whsle |
122,456,533 |
4,446,297 |
27.5 |
4228 |
Beer & ale whsle |
43,858,869 |
4,996,576 |
8.8 |
4229 |
Miscellaneous nondurable goods whsle |
112,711,142 |
13,198,232 |
8.5 |
Effective Warehouse Management

Simulation - Participation - Exercises - Implementation
|
Strategos Can Help To...
-
Design or improve your warehouse layout and operations for maximum efficiency.
-
Reduce inventory required and space required for its storage.
-
Improve customer response.
-
Reduce stockouts.
The Process Starts With...
1. A preliminary discussion that scopes the size and complexity of the problem.
2. A project discussion will follow in several days to, jointly, outline the scope of a
project that meets your needs and estimate preliminary costs. We will then send a proposal.
3. If you accept the proposal, we begin data acquisition and, together, execute the project.
Call me at 816-931-1414
Quarterman Lee
|
|
|