Feed and Speed Optimization
The intent is to show how AP-238 supports the refinement of
nominal machining process plans to generate optimized process plans given
better information just prior to machining. Extensions to the technological
parameters are proposed to handle the cutter cross sectional area. One aspect
of the demonstration is to validate these proposed extensions.
- We
start with an AP-238 program for 3-axis roughing of the Airbus fish head
part. There will be three versions of this, at least: Sandvik's large
tool, NIST's small tool, Boeing's medium-sized tool. The AP-238 program
will have resulted from one of those sites exporting AP-238 from their CAM
system.
- >The
AP-238 is run through the STEP-NC Explorer to generate NC code for the
target machine. Additionally, a STEP AP-203 or STL file is exported for
the starting stock.
- The
NC code and STEP or STL file are loaded into Vericut for a machining
simulation. Vericut outputs a sequence of cutter contact profiles as per
the “Digitized Cross-Sectional Area” slide in Leon Xu's presentation.
- The
Vericut output is loaded into a custom Boeing application that calculates
a series of six cross-sectional area parameters for each NC code line. The
result is a CSV file.
- The
CSV file is loaded into a (new) STEP merge process, which associates the
NC code line with the AP-238 toolpath, and inserts the tsix
cross-sectional area parameters into proposed extensions to the
technological parameters. An enhanced AP-238 program results.
- Just
prior to cutting, the enhanced AP-238 program is run through the STEP-NC
Explorer to generate NC code. The Explorer calls some Boeing optimization
algorithms that compute feeds and speeds based on requirements such as
minimize cutting time or maximize tool life. The result is an NC code
program optimized for the specific requirement.
|
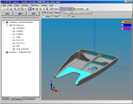
fishhead test part, showing the associated tolerances.
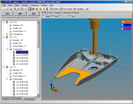
Tool information for fishhead test part, showing tool parameters
and associated machining workingsteps.
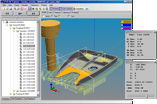
Toolpath and final geometry view of fishhead test part, showing
toolpaths with cross-section area information and feedrate boost.
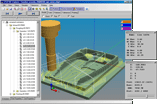
Cutting simulation view of fishhead test part at same point as
above, with cross-section area information and feedrate boost.
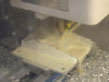
Machining of fishhead test part at Boeing Material & Process
Technology Lab, Renton, WA, on an OKUMA MC-V4020.
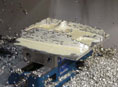
Completed fishhead test part machined at Boeing Material &
Process Technology Lab.
|